Introduction
In the foam industry, knowing different types of foam is important. This helps in choosing the right material for your project. Two popular foams are XPE and IXPE. XPE stands for Chemical Cross-linked Polyethylene Foam. IXPE stands for Irradiated Cross-linked Polyethylene Foam. They share similarities but have unique features. This article explains what XPE and IXPE are, how they are made, and their key differences. It will help you pick the best one for your needs.
What is XPE?
XPE is a Chemical Cross-linked Polyethylene Foam. It is a closed-cell foam. The “X” stands for its cross-linked structure. This structure is created using chemical agents during production. XPE is durable, water-resistant, and provides good thermal insulation. It also absorbs shocks well.
XPE is versatile and used in many industries, including:
- Insulation in buildings and HVAC systems
- Padding and cushioning in cars
- Sports mats and protective gear
- Packaging materials
What is IXPE?
IXPE means Irradiated Cross-linked Polyethylene Foam. Like XPE, it has a cross-linked, closed-cell structure. But its production process is different. Instead of chemicals, IXPE uses a physical process called irradiation. An electron accelerator irradiates the foam, creating the cross-links.
IXPE has several unique features:
- Smaller, more delicate cells for a smoother surface
- Better flexibility and impact resistance
- Enhanced thermal and acoustic insulation
These qualities make IXPE ideal for high-performance applications. Common uses include:
- Sound insulation in flooring
- High-quality packaging for fragile products
- Healthcare products and devices
- Protective layers in electronics and automotive parts
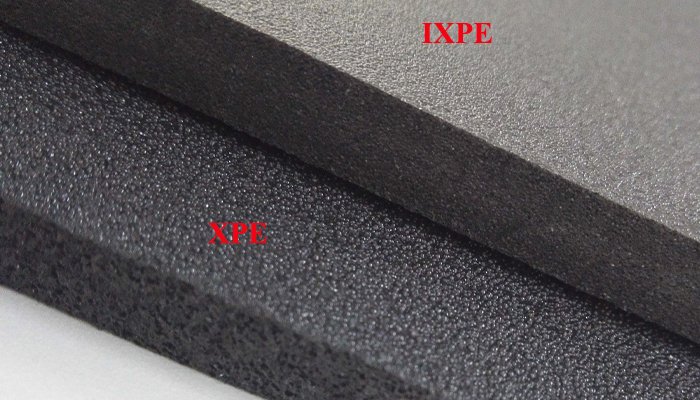
Production Process: XPE vs. IXPE
XPE and IXPE are both polyethylene foams. However, their production processes are different.
XPE Production Process:
XPE is made by mixing polyethylene with chemical cross-linking agents. The mixture is heated, causing the chemicals to start the cross-linking process. After the foam cross-links, it expands into a closed-cell structure. This process is simple, making XPE cost-effective.
IXPE Production Process:
IXPE does not use chemicals for cross-linking. Instead, it relies on irradiation. The foam is exposed to an electron beam, which causes the polyethylene chains to cross-link. The level of irradiation, along with factors like thickness and density, affects the foam’s final properties.
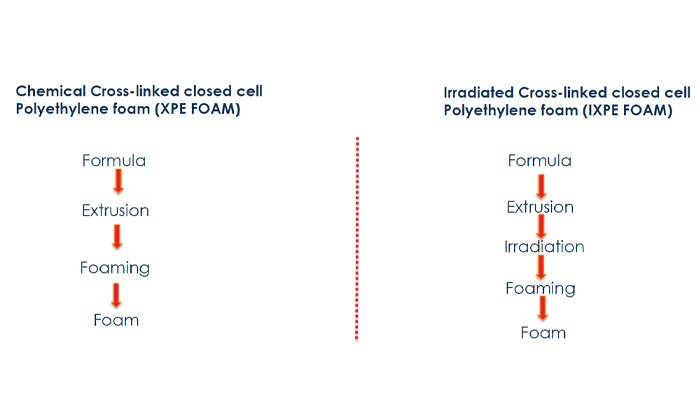
This method gives IXPE a smoother surface and finer cell structure. It results in better mechanical performance, making it a top choice for precision applications.
Key Differences Between XPE and IXPE
Feature
|
XPE
|
IXPE
|
---|---|---|
Production Process
|
Chemical cross-linking
|
Irradiation (physical cross-linking)
|
Cell Structure
|
Larger, more visible cells
|
Smaller, more delicate cells
|
Surface Texture
|
Rougher surface
|
Smoother, flatter surface
|
Mechanical Performance
|
Good, but less refined
|
Superior performance
|
Cost
|
More affordable
|
Higher cost due to irradiation
|
Common Applications
|
Construction insulation, car padding, sports mats
|
Sound insulation, high-end packaging, healthcare products
|
Advantages of XPE
XPE has many benefits, including:
- Cost-Effective: The chemical process is simple, so production costs are lower. This makes XPE more affordable than IXPE.
- Good Thermal Insulation: XPE is effective at preventing heat transfer. This is why it’s used in insulation.
- Water-Resistant: Its closed-cell structure keeps out water. This feature is great for insulation and packaging.
- Durable: XPE can withstand wear and tear. It is a good choice for automotive and construction uses.
Advantages of IXPE
IXPE offers several unique benefits, including:
- Smoother Surface Finish: The irradiation process creates a smoother, refined surface. This is important for applications needing a clean, polished finish.
- Better Mechanical Properties: IXPE has a finer cell structure. This provides better flexibility, cushioning, and impact resistance. It’s ideal for delicate packaging and protective layers.
- Improved Acoustic Insulation: The structure of IXPE is effective for sound insulation. It is widely used in flooring and automotive interiors.
- Chemical-Free Production: IXPE does not need chemical additives. This can be beneficial for applications where minimal chemical exposure is needed.
Choosing Between XPE and IXPE
When deciding between XPE and IXPE, consider these factors:
- Budget: If cost is important, XPE is more affordable. Its simple production process keeps prices low.
- Application Needs: If you need a smooth surface, better flexibility, or more impact resistance, choose IXPE. But if these are not priorities, XPE can still provide good performance at a lower cost.
- Performance: IXPE’s refined structure makes it suitable for high-precision uses. It’s a great choice for healthcare devices and products needing durability.
- Environment: IXPE’s irradiation process does not use chemicals. This makes it better for applications where chemical exposure should be minimized.
Conclusion
XPE and IXPE are high-quality polyethylene foams. Each has unique properties suited to different needs. XPE is economical, with good thermal insulation and water resistance. IXPE has superior mechanical properties, a smoother surface, and better acoustic performance. Knowing these differences can help you choose the right foam for your project.
If you are unsure which foam to choose, let us help. Share your requirements, and our team will recommend the best foam solution for your projects. needs, feel free to share your requirements with us. Our team is always here to help you make an informed decision and provide the ideal foam solution for your projects.